When there's no replacement within a 1000
nautical miles, count on APV Plate Heat
Exchangers to meet critical cooling needs.
Our compact, reliable Plate Heat Exchanger
(PHE) has become indispensable to the smooth
functioning of offshore rigs and thousands of
vessels - from supertankers to harbor tugs.
All modern ships have huge cooling requirements,
the greatest being the main engine's. With its
charging air cooler, cylinder water cooler and
lubrication oil cooler, it requires a total cooling
capacity equivalent to 25% of the fuel consumption's
energy content.
Plate coolers used by the offshore industry are
generally used for the same purposes as those
aboard ship, though they may be given additional
duties, such as cooling drilling oil, cabin heat,
tap water, etc.
|
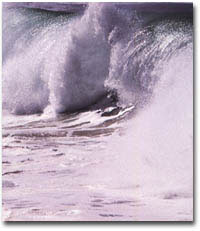
|
Ideally suited for sea duty
APV Plate Heat Exchangers have proved themselves to be perfect for
the closed circuit
systems essential to many cooling functions at sea. Using high purity
water as the primary
coolant eliminates erosion, corrosion and scaling problems in costly
equipment.
When sea water is used as the secondary coolant we use resistant metals
to counter
its destructiveness.
The high heat transfer coefficients of our PHEs produce minimum
temperature differences,
a vital consideration in closed loop cooling. The differences between
primary and
secondary coolants can generally be reduced to less than 5ºC, thereby
allowing maximum
cooling of the primary liquid.
We have over 60 years experiance in PHE technology. Always comitted to
research and
development, and to maintaining our industry leadership, we offer you
the most advanced
product and service programme available today.
You can count on APV
|
The 3 Basic Cooling systems
|
1. Direct sea-water cooling
Each of the ship coolers is connected
to the
sea-water system and is independently cooled directly
with sea water.
|
|
Click image for bigger size
|
Charging air coolers are placed first in the system - thus,
they will get the coldest water -
then the lubricating oil coolers and finally the fresh-water coolers for
main and auxiliary
engines. For slow-speed main engines with oil-cooled pistons there are
substantial
quantities of heat in the lubricating oil. In this case the lubricating
oil cooler should be
placed in parallel with the charging air cooler, other wise the oil
cooler will be oversized.
Direct sea-water cooling is in a short term the cheapest system - and
it is uncomplicated
to control.
The drawback is that the system contains a large number of long
sea-water tubes, which
are all exposed to corrosion. Therefore, cost for repair and
replacements must be taken
into account - this is also the case with coolers, which are not made of
titanium.
|
2. Central Cooling
In this system only one sea-water
cooler is used,
where fresh water is cooled to a temperature a few
degrees above sea-water temperature.
|
|
Click image for bigger size
|
This quantity of fresh water is used for the same purposes as the
sea-water cooled system.
The advantage of this system is that the corrosion damage is limited to
comparatively few
and short seawater tubes. Moreover all the coolers of the ship apart
from the big central
cooler can be produced in cheaper materials than titanium, as corrosion
in excluded.
Control of, the central cooling system is more complicated than the
direct sea-water
cooling system, due to here being two or more levels of temperature in
the same system.
For main engine with a water-cooled piston, the piston cooler must be
cooled separately,
as sea water must not be mixed with the cooling system.
|
3.Central cooling with separate
cylinder/piston cooling
The principle is the same as for
central cooling,
but differs by cylinders and pistons (only engines
with water-cooled pistons) having their own coolers,
|
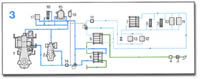 |
Click image for bigger size |
which
are cooled with sea water after the central cooler.
This gives a considerably smaller central cooler and advantages in
control.
The sea-water tube system will be
larger than in central cooling, but still it is
considerably simpler than in direct sea-water cooling.
|
Our compact, ready-to-install
sea water desalination unit for
ships and offshore rigs has
the heart of a PHE
|
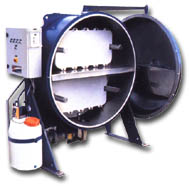 |
Available in 5
basic units with capacities from 4 to 60 tons
a day, our sea water desalination units are a natural extension
of the APV Plate Heat Exchanger programme.
To save space, the APV sea water
desalination units is
designed as a compact unit which at delivery is ready-
mounted with complete electric installation and piping system.
Ejector pump for mounting below the water line can also be
supplied. The APV unit needs a minimum of space in relation
to its capacity. |
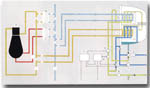
Click image for bigger Size
|
The design of the sea water desalination
unit is based on 2 APV Plate Heat Exchangers
functioning as an evaporator and a condenser, respectively. Both Plate
Heat Exchangers are as
standard fitted with plates of titanium. In the lower Plate Heat
Exchanger - the evaporator -
seawater is admitted and under vacuum caused evaporate.
In the upper Plate Heat Exchanger -
the condenser - the vapour from the evaporator condenses
into fresh water.
|
Design
Unit/Weight-Carrying frame:
Compact and rugged construction with a view to absorbing vibrations and
violent movements from
the ship. The vessel is made of stainless steel and painted blue.
The inspection hatch has a special
hang-up bracket and may easily be swung aside thus given
easy access to evaporator and condenser during cleaning and inspection.
|
Evaporator/Condenser
APV Plate Heat Exchangers with specially
formed 0,6 mm titanium plates. This special forming
quarantees a large flow area in one side of the Plate Heat Exchangers
for effective steam passage.
Gaskets of nitrile rubber are used.
|
Working
principle
The unit with evaporator and condenser
is put under vacuum by means of a seawater-driven
ejector pump. The absolute pressure must lie at approx. 0,1 bar. At this
pressure, seawater will
evaporate at approx. 40°C. The side of the evaporator plates opening
towards the vacuum tank is
fed with seawater. On the opposite side of the evaporator plates, engine
cooling water of 60-80°C
is circulated.
Some of the admitted seawater boils
when coming into contact with the hot plates and leaves
the evaporator as steam through the open side of the plate pack. The
remaining quantity of
seawater now containing a higher salt concentration (brine) is exhausted
overboard by the ejector.
The steam from the evaporator passes
through a demister to the condenser. The condenser is
constructed like the evaporator with an open side at the top towards the
vacuum tank, the opposite
side is totally closed. On the closed side, cold seawater is circulated.
When the steam makes
contact with the cold plates, it will condense. Normally, the condenser
is connected to the
ship - possibly to fresh water from the central cooling system of the
ship.
The processed (desalinated) water is
pumped to the processed water tanks of the ship, thereby
passing a sensor which is connected to a salinometer. The salinometer
measures the salinity of the
processed water. If the salinity is higher than the preset reference
value e.g. 5ppm - a solenoid
valve opens and the water is returned to the desalination unit. The
salinometer can be connected to
remote alarm so that too high a salinity can immediately be registered
at the bridge of the ship or in
the control room. |
APV sea-water
desalination plants are small
-but the advantages aren't |
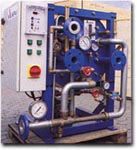 |
Resistance to corrosion
Evaporator and condenser are equipped with titanium plates. The only
material which in practice
has proven to be resistant to sea water even in polluted waters.
Compact construction
Plate Heat Exchangers- evaporator and condensers are effective and
very compact. The APV
sea-water desalination unit therefore has small installation dimensions
and can easily be placed
in a modern. densely packed engine room
Service requirement
Salt-water quantity/brine concentration are very carefully adjusted
in order to obtain minimum
scaling. The effective evaporator and the ejector keeps the evaporation temperature
at an
absolute minimum - i.e. 40°C at normal working conditions - which
reduces scaling. Moreover
boiling in the evaporator is of such a degree that a cleaning effect is
obtained. Cleaning once a year
is normally enough. By opening the front cover of the vacuum tank, the
evaporator and the
condenser are immediately accessible for possible separation and
cleaning. The titanium plates are
easily removable - weight 0,6 kg to 1,5 kg.
Operating economy
The APV sea-water desalination unit is mounted with a special
double-acting ejector requiring less
capacity on the ejector pump. This gives a reduction in the electric
generator effect thereby lowering
the fuel costs.
Non-standard plants
Besides our standard types of sea-water desalination units we can
supply a number of non-standard
designs, i.e. units for jacket-water temperatures as low as 50°C, units
for steam heating, units for
combined jacket-water/steam heating, units where the sea water for the condenser
is also led
through the ejector giving a simplified installation.
Additional equipment
Dosing equipment for inhibitors to reduce scaling in the evaporator;
filter for water hardening to
improve the taste of the produced fresh water; equipment for ultraviolet
water disinfection and
equipment for thermal disinfection. |
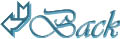 |