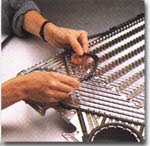 |
The exclusive Paraclip gasket
The glueless, easy-to-fit Paraclip gasket
offers the strength and security of
conventional gaskets in nearly all
applications. It can withstand pressures
up to 25 bar. Its special clip-on feature
locks it into recesses in the gasket groove.
No special skill is required to insert the
gasket or replace it. The Paraclip is
available in Nitrile and EPDM.
Other materials available on request.
|
The safeguard
APV gaskets are designed to give a double seal
at the ports. This keeps liquids from mixing.
A leak brought on by process abnormality (eg.
pressure shock) floods the dead space formed
by the doubleseal. It is led from there by drain
channelsto the outside, thus making the leak and
its source in the plate pack readily visible.
|
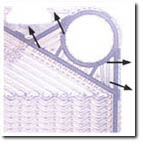 |
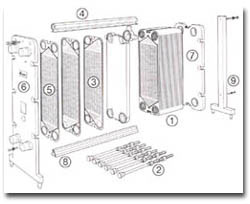 |
Parts Of a whole
- Plate pack
- Tie bolt
- Flow plate and gasket
- Hanging bar
- End plate
- Fixed head with inlet and outlet ports
- Follower with inlet and outlet ports
- Guide bar
- End support
|
Comparative space requirements
The PHE is only abaut 1/3 the size and 1/6
the weight of a tubular unit capable of comparable duty.
Where the PHE is a viable alternative to its tubular
counterpart, the cost savings begin even before the
PHE goes to work.
|
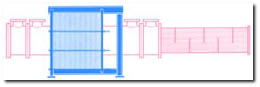 |
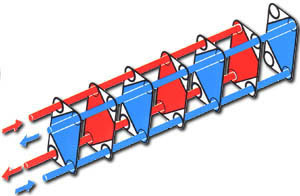 |
Regulating transmission and pressure drop
APV plates are available in thermally short (soft),
vertical and thermally long (hard) horizontal flow
profiles. The thermally long plate produces greater
turbulence and thereby higher transmission values
than the thermally short plate, the latter offers lower
pressure drop. By combining the two, optimal heat
transfer can be obtained at any pressure drop in a
manner suitable to process treatment and handling
needs of your product.
|
The flexibility offers creative opportunities for design engineers
Typical countercurrent flow
Complex flow patterns
By varying flow patterns and introducing morechannels, an
extraordinary number of configurations are
feasible. Anything from a singlepass countercurrent pattern, with just
two liquids, to a multipass pattern
using three or more liquids in asymmetric flows. The object of nay
design must of course be to achieve
the optimal balance of thermal transfer and pressure loss in any given
situation. The ease of changing
plate configurations makes the PHE highly adaptable to changing process
requirements. |
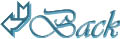 |